视觉引导型机器人金属薄板壳体装配
摘要
高精度金属薄板壳体装配需要花费大量劳动力。为降低装配成本并提高装配效率和质量,机器人凭借在速度、精度和灵活性方面的关键优势,已成为构建自动装配系统的不错选择。本文将介绍基于机器人的金属薄板壳体装配技术,以演示、验证和优化自动化大规模定制装配流程的关键解决方案。
问题陈述
高精度金属薄板壳体装配流程需要花费大量劳动力,需要超过 52 名操作员在该流程中紧张工作。如图 1 所示,分离器装配到底部壳体形成一个部件,然后该部件与反冲弹簧和顶部壳体装配在一起以装配壳体组件。显然,装配壳体时要非常小心,因为产品很容易变形和划损。金属薄板部件的厚度为 0.25 mm,装配精度小于 0.03 mm。此外,还有 100 多个产品部件号需要支持,图 1 所示产品是典型的 SFP+ 1X4 壳体产品,还有一些其他产品,如 1XN 和 2XN 分类的 SFP、SFP+、QSFP、ZQSFP 等产品系列。显然,实现壳体装配流程的自动化就是处理高混合和低容量质量定制自动化问题,而传统的硬工具自动化方法在这种情况下不适合大规模定制装配的要求。
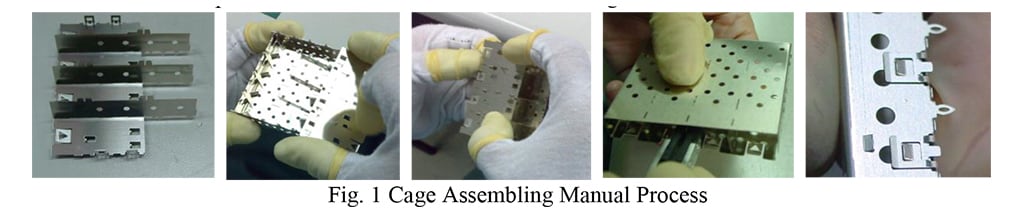
机器人凭借在速度、精度和灵活性方面的关键优势,已成为构建自动且灵活装配系统的不错选择。本调查研究探讨了机器人/机器人技术的有趣功能,并介绍了采用机器人技术的大规模定制金属薄板壳体装配流程的解决方案,这些解决方案可积极影响 TE 的业务并促进技术开发。为了提高机器人壳体装配系统的可靠性和稳健性,本调查研究还研究了装配流程的细节,并进行了两次实验设计 (DoE),以优化分离器和底部壳体装配以及顶部壳体和反冲弹簧装配。本调查研究开发的基于机器人的装配系统和装配流程优化方法有望应用于整个 TE 业务部门的其他产品装配流程,从而显著降低装配成本并提高装配效率和质量。
方法和结果
工业机器人简介
工业机器人通常是指 SCARA 机器人、6 轴机器人和 Delta 机器人。SCARA 机器人具有 3-DOF(自由度)平移和 1-DOF 旋转功能,通常用于执行取放操作;6 轴机器人具有 3-DOF 平移和 3-DOF 旋转功能,可广泛用于各种制造和装配流程中。Delta 机器人是并行架构,一般具有 3-DOF 平移和 1-DOF 旋转功能,通常用于执行快速取放操作。对于金属薄板装配流程,分离器和顶部壳体的装配需要对部件进行平移和旋转,以沿着装配路径完成装配,因此在这种情况下建议使用 6 轴机器人。图 2 所示为典型的 6 轴机器人和机器人架构,用于研究机器人末端执行器的移动性。6 轴工业机器人也称为 6-R 机制(R:旋转接头),可进一步分解成两部分:机械臂和机械手腕。机械臂可实现 3-DOF 平移,机械手腕可实现 3-DOF 旋转。通过机械臂和机械手腕之间的协调,机器人末端执行器能够在其工作空间内达到任何定义的位姿,并将能够非常敏捷地完成金属薄板壳体装配流程。
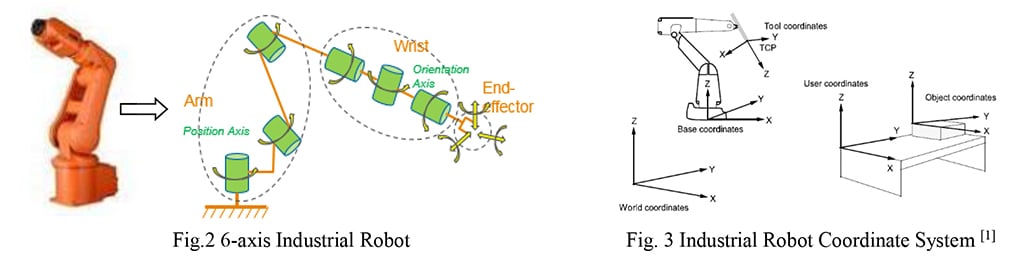
通过建模和控制方法以及良好的机器人编程语言和编程接口,工业机器人现已取得长足的发展。最终用户不必研究电机控制、正向运动学/逆向运动学甚至动力学的细节。但是有必要使用机器人编程语言开发一些有关机器人运动和路径规划的技术。将末端执行器安装到机器人上后,将基于机器人工具坐标(将在机器人末端执行器中定义并与之相连)来规划运动和路径。图 3 说明了关键机器人坐标系的一些概念。机器人路径的精确控制是精确控制关键的机器人目标。特别是在壳体装配流程中,构建机器人装配路径的步骤可能是线性平移或旋转,甚至是两者的组合,为了构建平稳的装配路径以避免任何干扰,精确定义机器人步数至关重要。对于每个机器人目标,机器人末端执行器应在其位置 (x, y, z) 和方向 (Ex, Ey, Ez) 中精确定义,其中 x、y、z 是关于对象坐标系的坐标,Ex、Ey、Ez 是关于对象坐标系的欧拉角。
视觉引导型机器人
对于高精度装配,传统的自动化方法是设计和制造高精度机械夹具以进行部件定位,并开发高精度机械装置以进行部件装载和装配,这对机械系统保持精度提出了挑战。采用视觉引导型机器人方法时,将视觉系统集成为机器人系统的一部分,以精确识别机器人工具上夹住部件的位姿,然后机器人/机器人工具根据视觉识别反馈,对部件进行自适应平移或旋转,以确保装配精度。
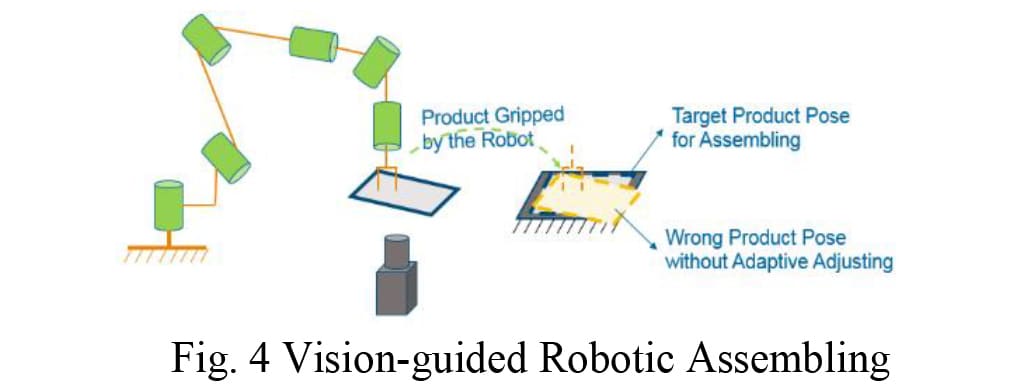
图 4 所示为一个用于自适应装配/取放操作的典型视觉引导型机器人系统。由于一些定位错误,机器人可能无法在同一位置或方向拾取产品,机器人示教产生的恒定机器人位姿可能无法装配产品,视觉系统将非常有助于引导机器人自适应地调整装配路径,以保证装配系统的可靠性和稳健性。
开发机器人自适应装配算法的过程是先创建基本模型作为参考模型,然后制定目标位姿计算模型,对机器人位姿进行自适应调整,实现对产品的精确装配。通过计算用于捕捉图像的机器人位姿 (XRb, YRb, ARb)、通过 2D 视觉系统在机器人工具中识别的产品位姿 (XCb, YCb, ACb) 以及作为参考基础的用于精确装配产品的示教位姿 (XFb, YFb, AFb) 来创建基本模型。根据参考基础可计算出产品目标位姿 (XCFb, YCFb, ACFb)。显然,为了精确装配产品,产品目标位姿保持恒定。这里的 X/Y 表示位置,A 表示沿 z 轴的旋转角度,由于使用的是 2D 视觉系统,本文研究了 2D 平面上的位姿分量。
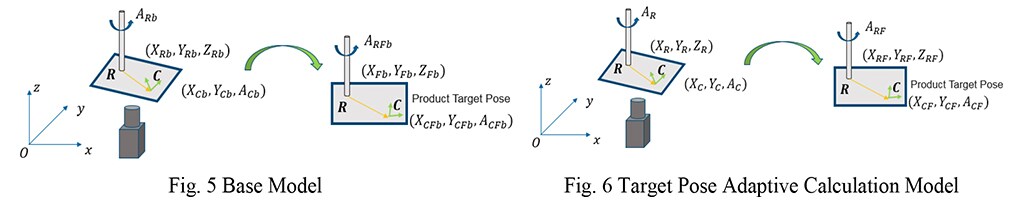
如图 4 所示,机器人工具在点 R 处夹持产品,而表示机器人工具中产品位置和方向的特性为框架 C,已知用于装配产品机器人示教位姿,根据矢量 𝒗𝑟𝑐 从图像捕捉位姿到装配位姿和机器人示教位姿的平面转换计算产品装配的产品目标位置,以装配产品。因此,产品目标位置用公式表示为:

其中,𝒗𝑟𝑐 = (𝑋𝐶𝑏 − 𝑋𝑅𝑏, 𝑌𝐶𝑏 − 𝑌𝑅𝑏)𝑇。
根据产品特性方向 ACb 和机器人的旋转变化 ∆𝐴𝑏 = 𝐴𝑅𝐹𝑏 − 𝐴𝑅𝑏, 计算用于产品装配的产品目标方向以作为 Eq. (2):
𝐴𝐶𝐹𝑏 = 𝐴𝐶𝑏 + ∆𝐴𝑏 (2)
使用图 6 所示的模型用公式表示用于装配产品的自适应机器人目标位姿,很容易知道产品目标位姿,因为它与参考基准相同:
𝑋𝐶𝐹 = 𝑋𝐶𝐹𝑏, 𝑌𝐶𝐹 = 𝑌𝐶𝐹𝑏, 𝐴𝐶𝐹 = 𝐴𝐶𝐹𝑏 (3)
用于捕捉图像的机器人位姿为 (XR, YR, AR),机器人工具处识别的产品位姿为 (XC, YC, AC),并且从图像捕捉位姿到装配位姿的产品旋转角度的变化用公式表示为 Eq. (4):
∆A = 𝐴𝐶𝐹 − 𝐴𝐶 (4)
因此,使用识别的产品特性方向自适应计算用于装配产品的目标机器人方向以作为 Eq. (5):
𝐴𝑅𝐹 = 𝐴𝑅 + ∆𝐴 = 𝐴𝑅 + 𝐴𝐶𝐹 − 𝐴𝐶 (5)
根据矢量 𝒗𝑟𝑐 和产品目标位姿的平面转换,用公式表示用于产品装配的目标机器人位置以作为 Eq. (6):

其中,𝒗𝑟𝑐 = (𝑋C − 𝑋R, 𝑌C − 𝑌R)T
通过视觉系统精确识别图 5 和图 6 所示的产品特性,精确装配产品的机器人位姿不是恒定的位姿,而是根据 Eq. (5) 和 Eq. (6) 用公式表示的自适应机器人位姿。
对于金属薄板壳体装配流程,分离器和反冲弹簧的机械定位精确度约为 0.3 mm,顶部壳体的机械定位精确度在位置上约为 0.1 mm,在方向上约为 0.25 度。为满足 0.03 mm 的装配精度,集成了定位精度为 +/-0.003 mm 的视觉系统,以自适应地引导机器人,如图 8 所示。结合 +/-0.01 mm 的机器人重复性,机器人系统进行装配的整体精确度约为 0.02 mm,足以完成金属薄板壳体装配流程。
机器人金属薄板壳体装配系统
为了开发大规模定制自动化系统,以涵盖高混合和低容量壳体产品的高精度装配,金属薄板壳体装配系统(见图 7-a)包含一个用于执行部件装载和装配的 6 轴机器人,以及一个用于精确识别机器人工具和装配固定装置所夹持部件位姿的视觉系统。机器人配备两个机器人工具,一个是用于执行分离器和反冲弹簧的装载和装配的气动夹子,另一个是用于装载和装配底部壳体和顶部壳体的气动吸盘。装配固定装置由分离器装配站与顶部壳体和反冲弹簧装配站之间的线性螺丝运送。
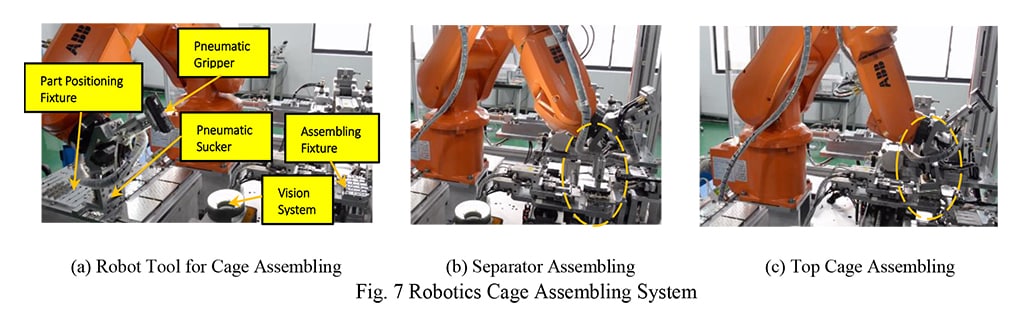
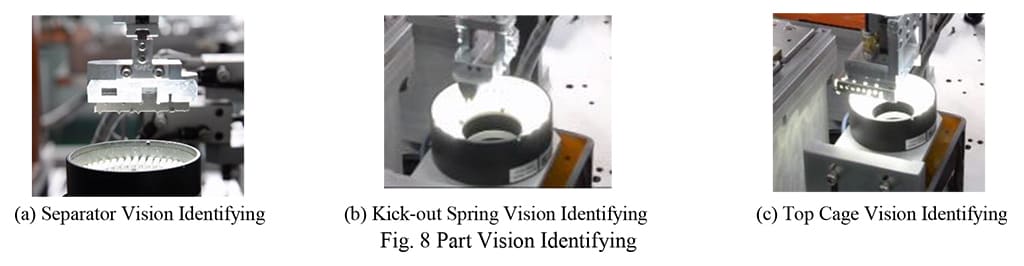
机器人首先将底部壳体装载到分离器装配站的装配固定装置,然后分别用底部壳体装载和装配分离器以形成一个部件,如图 7-b 所示。然后,线性螺丝将带有该部件的装配固定装置运送到反冲弹簧和顶部壳体装配站,在其中对装配固定装置精确定位,并且通过用于反冲弹簧和顶部装配的分离器固定装置将分离器精确固定,如图 7-c 所示。通过视觉系统精确识别机器人工具处夹持部件的位姿,根据 Eq. (5) 和 Eq. (6) 推导的公式,对分离器、反冲弹簧和顶部壳体进行自适应装配。
机器人装配流程优化
为了提高可靠性并尽可能提高机器人金属薄板壳体装配系统的能力,我们进行了两次实验设计 (DoE) 以优化装配流程,一次 DoE 针对分离器和底部壳体装配,另一次 DoE 针对反冲弹簧和顶部装配。高精度装配流程的关键因素通常是装配固定装置的部件定位机制以及机器人装配路径。
对于分离器和底部壳体装配流程优化,底部壳体处于良好位置,并由装配固定装置的定位机制固定。经验证,用于分离器装配的装配固定装置的问题并不大,已选择另外两个因素(装配速度和装配路径)来优化成品率,而图 9-a 所示的帕累托图表明装配路径是影响装配成品率的重要因素。最佳分离器装配成品率已达 97%,最佳分离器装配路径如图 10-a 和图 10-b 所示。由于分离器结构的差异,分离器 1 的装配路径与分离器 2 和 3 的路径不同,以避免对底部壳体产生任何干扰。
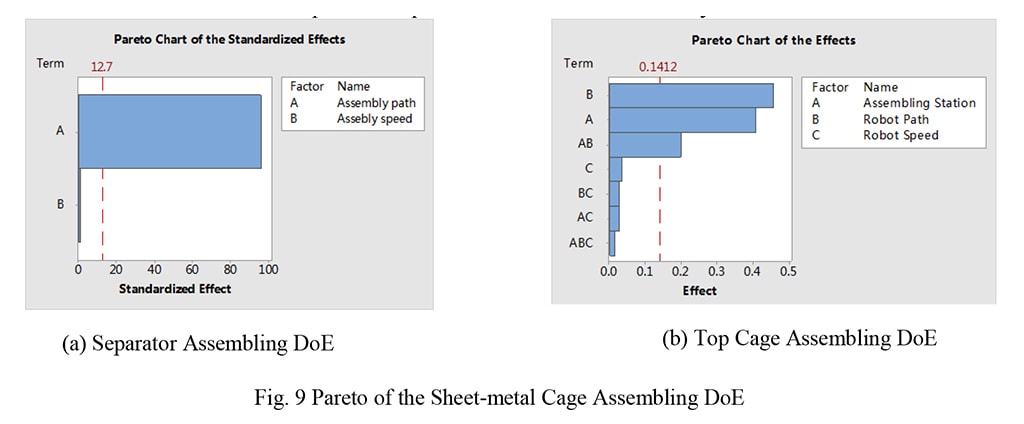
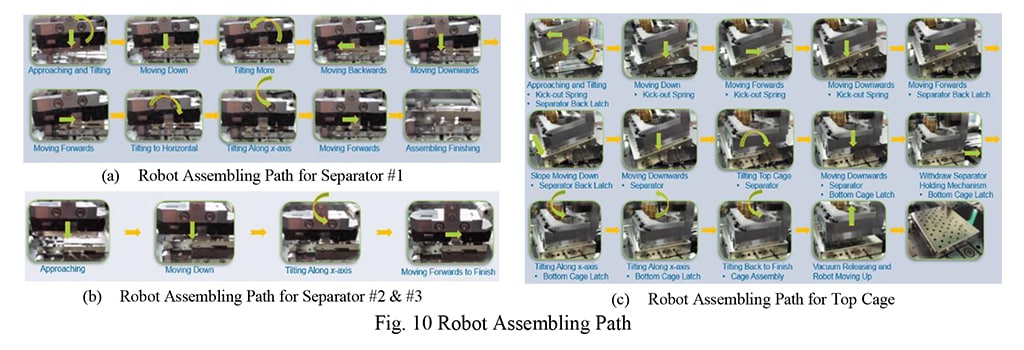
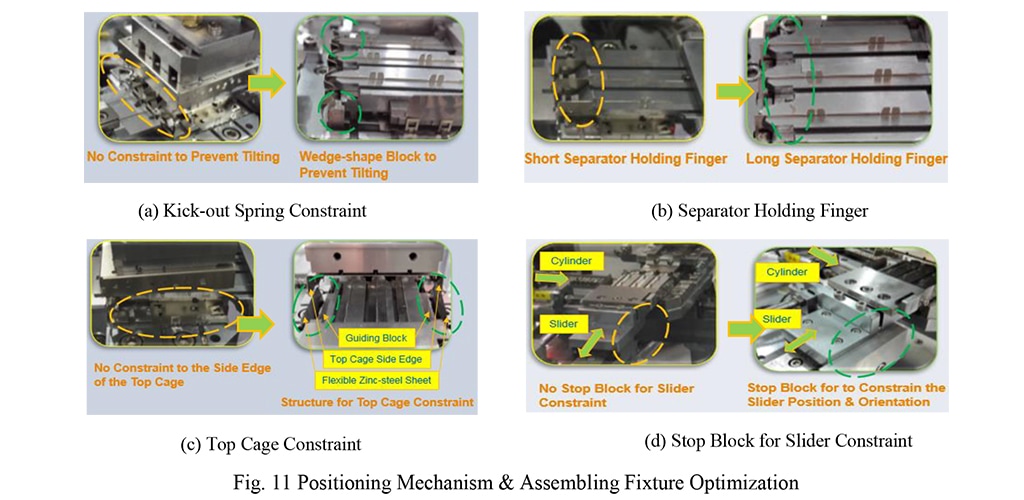
对于顶部壳体装配优化,已选择三个因素执行组装 DoE,而图 9-b 所示的帕累托图表明机器人路径、装配固定装置和定位机制以及两个因素的相互作用是影响因素。最佳顶部壳体装配成品率已达 97%,最佳顶部壳体装配路径如图 10-c 所示,最佳定位机制和装配固定装置如图 11 所示。由于顶部壳体必须与反冲弹簧、分离器和底部壳体良好适配才能成功装配,因此每个最佳装配步骤都经过精心设计,考虑到了各关键项。对于与机器人装配路径协调以提高装配成品率的定位机制和装配固定装置优化,反冲弹簧约束已得到改进,受一对楔形块约束,以避免弹簧因顶部壳体的任何轻微作用力而倾斜,这可能会导致顶部壳体装配 NG,如图 11-a 所示。分离器夹持指已改进为更长的指状物,能够紧紧且精确地夹持分离器,以避免在高速分离器中出现任何振动,如图 11-b 所示。通过使用导丝板和柔性镀锌钢板约束侧边,改进了顶部壳体约束,确保顶部壳体两个侧边之间距离的较大容差 (-0.1~0.7 mm) 的兼容性,如图 11-c 所示。考虑到滑块与用于进给和收回分离器夹持指的引导轨道之间的间隙,并使用气动气缸按压分离器夹持指以紧紧地固定分离器,分离器和底部壳体可能有一些位置和旋转误差。添加一个停止块以约束滑块的位置和方向,保证装配站分离器和底部壳体的定位精确度,这对于装配的可靠性和稳健性至关重要,如图 11-d 所示。
在不降低装配成品率的情况下,通过优化机器人速度,装配效率也有所提高。表1 显示了装配每个部件的最佳周期时间,其中机器人行进速度优化为 2,000 mm/s,分离器和反冲弹簧装配的机器人速度优化为 50 mm/s,顶部壳体装配的机器人速度优化为 30 mm/s。最佳周期时间满足壳体装配流程工业化的要求。
表 1
装配项目 | 底部壳体 | 分离器 1 | 分离器 2 | 分离器 3 | 反冲弹簧 | 顶部壳体 |
周期时间 (s/pcs) | 2.2 | 4.6 | 3.2 | 3.4 | 4.0 | 7.0 |
讨论及要点
金属薄板壳体装配的生产机器开发
本调查研究对基于机器人的金属薄板壳体装配进行了可行性验证,并对装配流程优化进行了两次 DoE,改善了装配成品率和装配周期时间。显然,该技术已验证达到工业化目标,DoE 平台已转移到 D&D 珠海工厂进行批量生产,最新生产数据显示,该平台的成品率为 98%,节约了 4 名操作员的劳动力成本(每年节约成本 48,000 美元)。下一步是构金属薄板壳体装配的生产机器,可以预见,实施采用这项技术的生产机器,每年可为 TE D&D 业务部门节约 52 万美元的劳动力成本。此外,这里开发的基于机器人的金属薄板壳体装配技术将显著提高 TE 在高精度水平大规模定制装配的能力,这种能力可以转而支持汽车、工业、CPD、传感器等其他业务部门的大规模定制装配自动化的发展,这肯定会在整个 TE 中产生巨大的业务影响。
致谢
开发基于机器人的金属薄板壳体装配技术是一段激动人心的旅程,开发人员非常感谢来自 TE 全球运营和 D&D 业务部门负责人的支持和赞助,特别是 Philip Gilchrist、Darel Callis、Rolando Saavedra 和 Marshall Chen 的有益建议和指导。
参考
[1] 技术参考手册 – RAPID 指令、功能和数据类型,ABB 机器人文档 M2004,rev H,RW5.15
视觉引导型机器人金属薄板壳体装配
摘要
高精度金属薄板壳体装配需要花费大量劳动力。为降低装配成本并提高装配效率和质量,机器人凭借在速度、精度和灵活性方面的关键优势,已成为构建自动装配系统的不错选择。本文将介绍基于机器人的金属薄板壳体装配技术,以演示、验证和优化自动化大规模定制装配流程的关键解决方案。
问题陈述
高精度金属薄板壳体装配流程需要花费大量劳动力,需要超过 52 名操作员在该流程中紧张工作。如图 1 所示,分离器装配到底部壳体形成一个部件,然后该部件与反冲弹簧和顶部壳体装配在一起以装配壳体组件。显然,装配壳体时要非常小心,因为产品很容易变形和划损。金属薄板部件的厚度为 0.25 mm,装配精度小于 0.03 mm。此外,还有 100 多个产品部件号需要支持,图 1 所示产品是典型的 SFP+ 1X4 壳体产品,还有一些其他产品,如 1XN 和 2XN 分类的 SFP、SFP+、QSFP、ZQSFP 等产品系列。显然,实现壳体装配流程的自动化就是处理高混合和低容量质量定制自动化问题,而传统的硬工具自动化方法在这种情况下不适合大规模定制装配的要求。
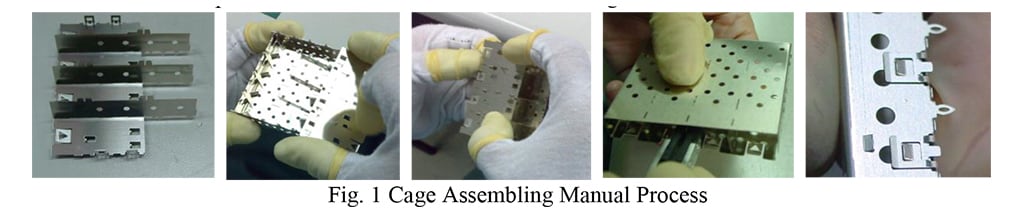
机器人凭借在速度、精度和灵活性方面的关键优势,已成为构建自动且灵活装配系统的不错选择。本调查研究探讨了机器人/机器人技术的有趣功能,并介绍了采用机器人技术的大规模定制金属薄板壳体装配流程的解决方案,这些解决方案可积极影响 TE 的业务并促进技术开发。为了提高机器人壳体装配系统的可靠性和稳健性,本调查研究还研究了装配流程的细节,并进行了两次实验设计 (DoE),以优化分离器和底部壳体装配以及顶部壳体和反冲弹簧装配。本调查研究开发的基于机器人的装配系统和装配流程优化方法有望应用于整个 TE 业务部门的其他产品装配流程,从而显著降低装配成本并提高装配效率和质量。
方法和结果
工业机器人简介
工业机器人通常是指 SCARA 机器人、6 轴机器人和 Delta 机器人。SCARA 机器人具有 3-DOF(自由度)平移和 1-DOF 旋转功能,通常用于执行取放操作;6 轴机器人具有 3-DOF 平移和 3-DOF 旋转功能,可广泛用于各种制造和装配流程中。Delta 机器人是并行架构,一般具有 3-DOF 平移和 1-DOF 旋转功能,通常用于执行快速取放操作。对于金属薄板装配流程,分离器和顶部壳体的装配需要对部件进行平移和旋转,以沿着装配路径完成装配,因此在这种情况下建议使用 6 轴机器人。图 2 所示为典型的 6 轴机器人和机器人架构,用于研究机器人末端执行器的移动性。6 轴工业机器人也称为 6-R 机制(R:旋转接头),可进一步分解成两部分:机械臂和机械手腕。机械臂可实现 3-DOF 平移,机械手腕可实现 3-DOF 旋转。通过机械臂和机械手腕之间的协调,机器人末端执行器能够在其工作空间内达到任何定义的位姿,并将能够非常敏捷地完成金属薄板壳体装配流程。
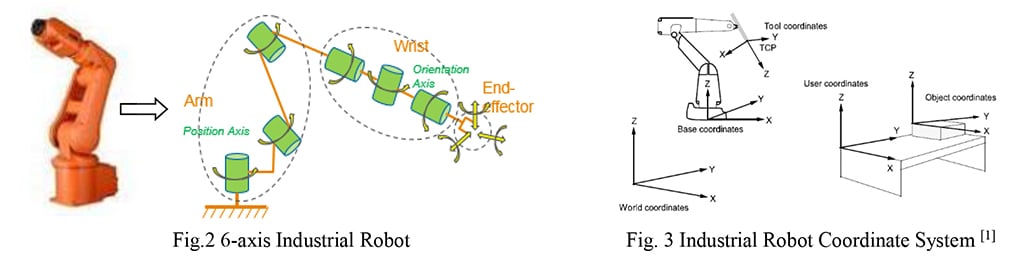
通过建模和控制方法以及良好的机器人编程语言和编程接口,工业机器人现已取得长足的发展。最终用户不必研究电机控制、正向运动学/逆向运动学甚至动力学的细节。但是有必要使用机器人编程语言开发一些有关机器人运动和路径规划的技术。将末端执行器安装到机器人上后,将基于机器人工具坐标(将在机器人末端执行器中定义并与之相连)来规划运动和路径。图 3 说明了关键机器人坐标系的一些概念。机器人路径的精确控制是精确控制关键的机器人目标。特别是在壳体装配流程中,构建机器人装配路径的步骤可能是线性平移或旋转,甚至是两者的组合,为了构建平稳的装配路径以避免任何干扰,精确定义机器人步数至关重要。对于每个机器人目标,机器人末端执行器应在其位置 (x, y, z) 和方向 (Ex, Ey, Ez) 中精确定义,其中 x、y、z 是关于对象坐标系的坐标,Ex、Ey、Ez 是关于对象坐标系的欧拉角。
视觉引导型机器人
对于高精度装配,传统的自动化方法是设计和制造高精度机械夹具以进行部件定位,并开发高精度机械装置以进行部件装载和装配,这对机械系统保持精度提出了挑战。采用视觉引导型机器人方法时,将视觉系统集成为机器人系统的一部分,以精确识别机器人工具上夹住部件的位姿,然后机器人/机器人工具根据视觉识别反馈,对部件进行自适应平移或旋转,以确保装配精度。
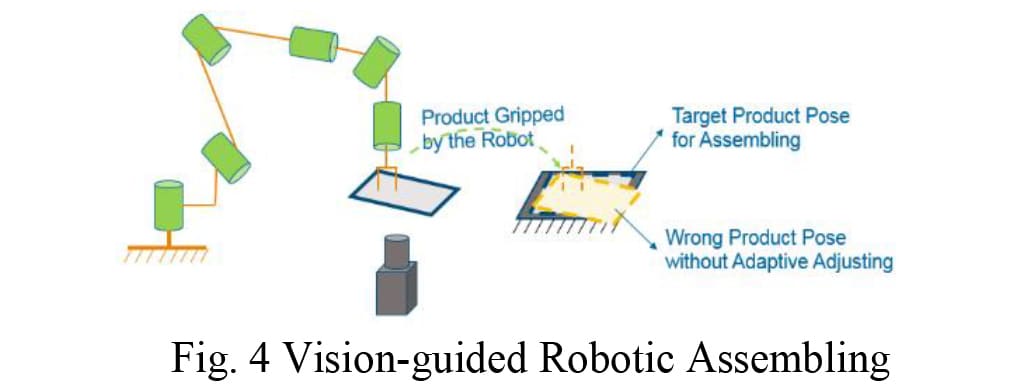
图 4 所示为一个用于自适应装配/取放操作的典型视觉引导型机器人系统。由于一些定位错误,机器人可能无法在同一位置或方向拾取产品,机器人示教产生的恒定机器人位姿可能无法装配产品,视觉系统将非常有助于引导机器人自适应地调整装配路径,以保证装配系统的可靠性和稳健性。
开发机器人自适应装配算法的过程是先创建基本模型作为参考模型,然后制定目标位姿计算模型,对机器人位姿进行自适应调整,实现对产品的精确装配。通过计算用于捕捉图像的机器人位姿 (XRb, YRb, ARb)、通过 2D 视觉系统在机器人工具中识别的产品位姿 (XCb, YCb, ACb) 以及作为参考基础的用于精确装配产品的示教位姿 (XFb, YFb, AFb) 来创建基本模型。根据参考基础可计算出产品目标位姿 (XCFb, YCFb, ACFb)。显然,为了精确装配产品,产品目标位姿保持恒定。这里的 X/Y 表示位置,A 表示沿 z 轴的旋转角度,由于使用的是 2D 视觉系统,本文研究了 2D 平面上的位姿分量。
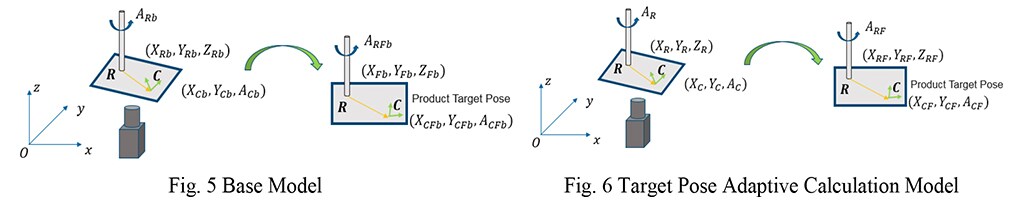
如图 4 所示,机器人工具在点 R 处夹持产品,而表示机器人工具中产品位置和方向的特性为框架 C,已知用于装配产品机器人示教位姿,根据矢量 𝒗𝑟𝑐 从图像捕捉位姿到装配位姿和机器人示教位姿的平面转换计算产品装配的产品目标位置,以装配产品。因此,产品目标位置用公式表示为:

其中,𝒗𝑟𝑐 = (𝑋𝐶𝑏 − 𝑋𝑅𝑏, 𝑌𝐶𝑏 − 𝑌𝑅𝑏)𝑇。
根据产品特性方向 ACb 和机器人的旋转变化 ∆𝐴𝑏 = 𝐴𝑅𝐹𝑏 − 𝐴𝑅𝑏, 计算用于产品装配的产品目标方向以作为 Eq. (2):
𝐴𝐶𝐹𝑏 = 𝐴𝐶𝑏 + ∆𝐴𝑏 (2)
使用图 6 所示的模型用公式表示用于装配产品的自适应机器人目标位姿,很容易知道产品目标位姿,因为它与参考基准相同:
𝑋𝐶𝐹 = 𝑋𝐶𝐹𝑏, 𝑌𝐶𝐹 = 𝑌𝐶𝐹𝑏, 𝐴𝐶𝐹 = 𝐴𝐶𝐹𝑏 (3)
用于捕捉图像的机器人位姿为 (XR, YR, AR),机器人工具处识别的产品位姿为 (XC, YC, AC),并且从图像捕捉位姿到装配位姿的产品旋转角度的变化用公式表示为 Eq. (4):
∆A = 𝐴𝐶𝐹 − 𝐴𝐶 (4)
因此,使用识别的产品特性方向自适应计算用于装配产品的目标机器人方向以作为 Eq. (5):
𝐴𝑅𝐹 = 𝐴𝑅 + ∆𝐴 = 𝐴𝑅 + 𝐴𝐶𝐹 − 𝐴𝐶 (5)
根据矢量 𝒗𝑟𝑐 和产品目标位姿的平面转换,用公式表示用于产品装配的目标机器人位置以作为 Eq. (6):

其中,𝒗𝑟𝑐 = (𝑋C − 𝑋R, 𝑌C − 𝑌R)T
通过视觉系统精确识别图 5 和图 6 所示的产品特性,精确装配产品的机器人位姿不是恒定的位姿,而是根据 Eq. (5) 和 Eq. (6) 用公式表示的自适应机器人位姿。
对于金属薄板壳体装配流程,分离器和反冲弹簧的机械定位精确度约为 0.3 mm,顶部壳体的机械定位精确度在位置上约为 0.1 mm,在方向上约为 0.25 度。为满足 0.03 mm 的装配精度,集成了定位精度为 +/-0.003 mm 的视觉系统,以自适应地引导机器人,如图 8 所示。结合 +/-0.01 mm 的机器人重复性,机器人系统进行装配的整体精确度约为 0.02 mm,足以完成金属薄板壳体装配流程。
机器人金属薄板壳体装配系统
为了开发大规模定制自动化系统,以涵盖高混合和低容量壳体产品的高精度装配,金属薄板壳体装配系统(见图 7-a)包含一个用于执行部件装载和装配的 6 轴机器人,以及一个用于精确识别机器人工具和装配固定装置所夹持部件位姿的视觉系统。机器人配备两个机器人工具,一个是用于执行分离器和反冲弹簧的装载和装配的气动夹子,另一个是用于装载和装配底部壳体和顶部壳体的气动吸盘。装配固定装置由分离器装配站与顶部壳体和反冲弹簧装配站之间的线性螺丝运送。
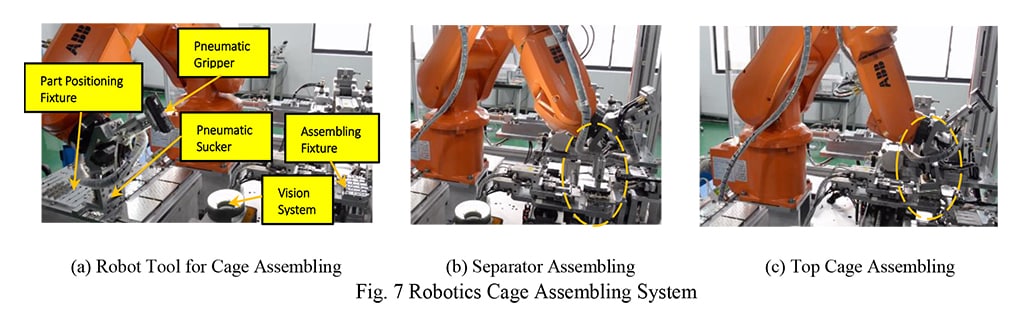
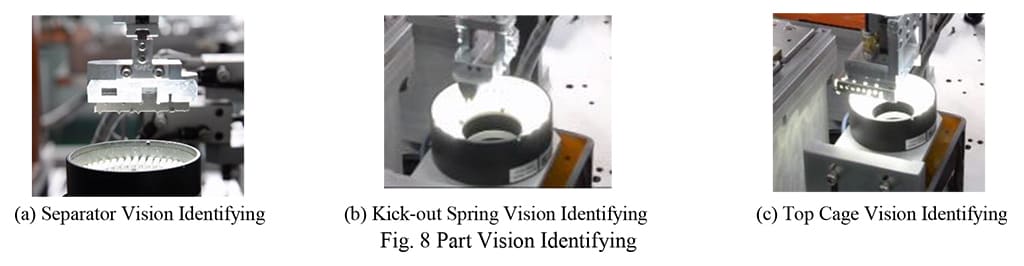
机器人首先将底部壳体装载到分离器装配站的装配固定装置,然后分别用底部壳体装载和装配分离器以形成一个部件,如图 7-b 所示。然后,线性螺丝将带有该部件的装配固定装置运送到反冲弹簧和顶部壳体装配站,在其中对装配固定装置精确定位,并且通过用于反冲弹簧和顶部装配的分离器固定装置将分离器精确固定,如图 7-c 所示。通过视觉系统精确识别机器人工具处夹持部件的位姿,根据 Eq. (5) 和 Eq. (6) 推导的公式,对分离器、反冲弹簧和顶部壳体进行自适应装配。
机器人装配流程优化
为了提高可靠性并尽可能提高机器人金属薄板壳体装配系统的能力,我们进行了两次实验设计 (DoE) 以优化装配流程,一次 DoE 针对分离器和底部壳体装配,另一次 DoE 针对反冲弹簧和顶部装配。高精度装配流程的关键因素通常是装配固定装置的部件定位机制以及机器人装配路径。
对于分离器和底部壳体装配流程优化,底部壳体处于良好位置,并由装配固定装置的定位机制固定。经验证,用于分离器装配的装配固定装置的问题并不大,已选择另外两个因素(装配速度和装配路径)来优化成品率,而图 9-a 所示的帕累托图表明装配路径是影响装配成品率的重要因素。最佳分离器装配成品率已达 97%,最佳分离器装配路径如图 10-a 和图 10-b 所示。由于分离器结构的差异,分离器 1 的装配路径与分离器 2 和 3 的路径不同,以避免对底部壳体产生任何干扰。
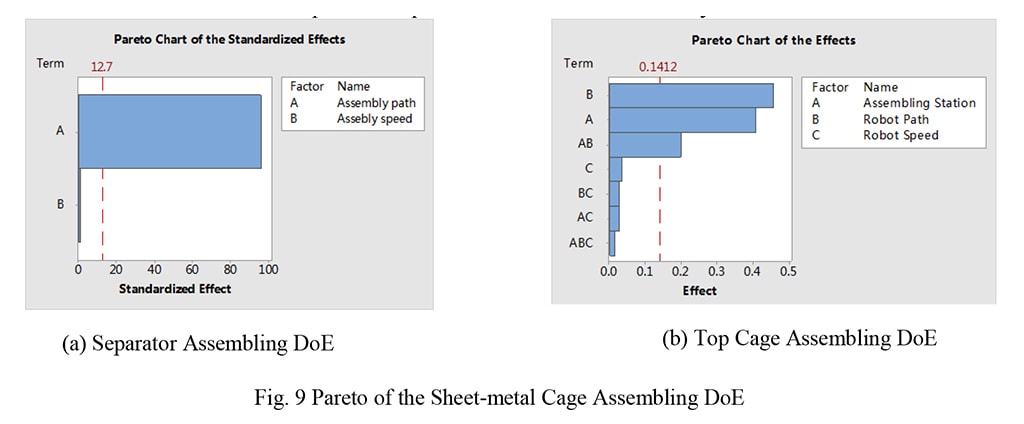
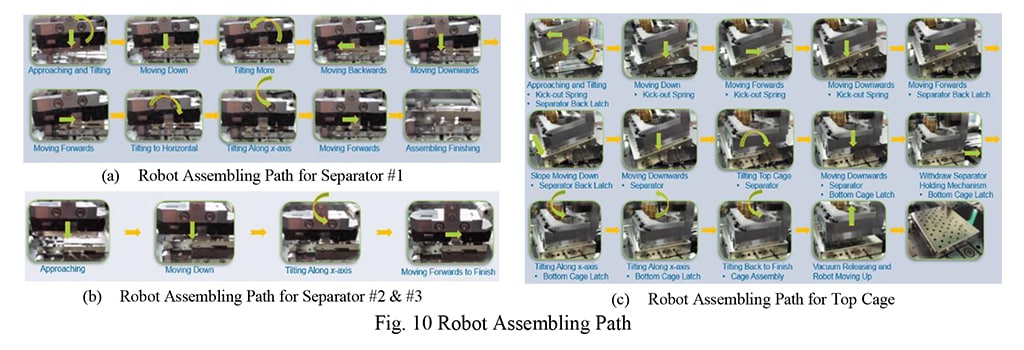
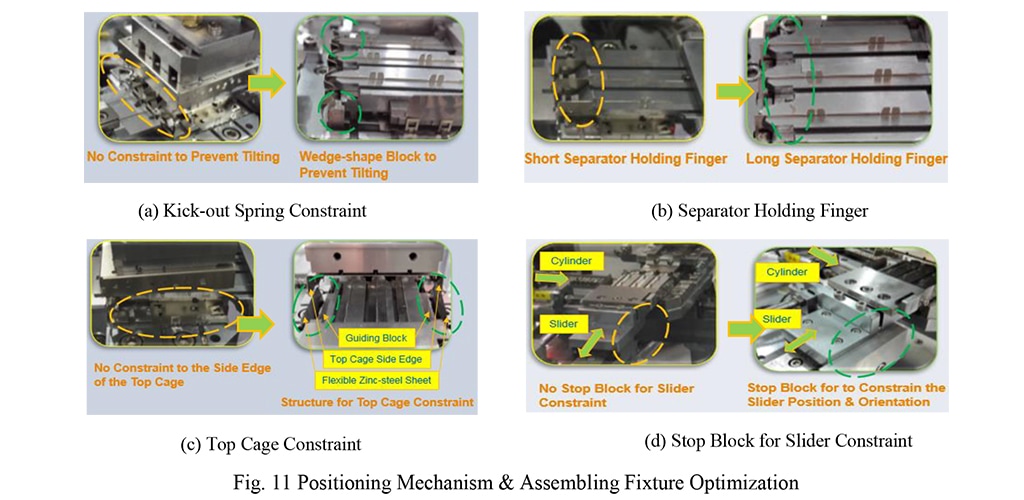
对于顶部壳体装配优化,已选择三个因素执行组装 DoE,而图 9-b 所示的帕累托图表明机器人路径、装配固定装置和定位机制以及两个因素的相互作用是影响因素。最佳顶部壳体装配成品率已达 97%,最佳顶部壳体装配路径如图 10-c 所示,最佳定位机制和装配固定装置如图 11 所示。由于顶部壳体必须与反冲弹簧、分离器和底部壳体良好适配才能成功装配,因此每个最佳装配步骤都经过精心设计,考虑到了各关键项。对于与机器人装配路径协调以提高装配成品率的定位机制和装配固定装置优化,反冲弹簧约束已得到改进,受一对楔形块约束,以避免弹簧因顶部壳体的任何轻微作用力而倾斜,这可能会导致顶部壳体装配 NG,如图 11-a 所示。分离器夹持指已改进为更长的指状物,能够紧紧且精确地夹持分离器,以避免在高速分离器中出现任何振动,如图 11-b 所示。通过使用导丝板和柔性镀锌钢板约束侧边,改进了顶部壳体约束,确保顶部壳体两个侧边之间距离的较大容差 (-0.1~0.7 mm) 的兼容性,如图 11-c 所示。考虑到滑块与用于进给和收回分离器夹持指的引导轨道之间的间隙,并使用气动气缸按压分离器夹持指以紧紧地固定分离器,分离器和底部壳体可能有一些位置和旋转误差。添加一个停止块以约束滑块的位置和方向,保证装配站分离器和底部壳体的定位精确度,这对于装配的可靠性和稳健性至关重要,如图 11-d 所示。
在不降低装配成品率的情况下,通过优化机器人速度,装配效率也有所提高。表1 显示了装配每个部件的最佳周期时间,其中机器人行进速度优化为 2,000 mm/s,分离器和反冲弹簧装配的机器人速度优化为 50 mm/s,顶部壳体装配的机器人速度优化为 30 mm/s。最佳周期时间满足壳体装配流程工业化的要求。
表 1
装配项目 | 底部壳体 | 分离器 1 | 分离器 2 | 分离器 3 | 反冲弹簧 | 顶部壳体 |
周期时间 (s/pcs) | 2.2 | 4.6 | 3.2 | 3.4 | 4.0 | 7.0 |
讨论及要点
金属薄板壳体装配的生产机器开发
本调查研究对基于机器人的金属薄板壳体装配进行了可行性验证,并对装配流程优化进行了两次 DoE,改善了装配成品率和装配周期时间。显然,该技术已验证达到工业化目标,DoE 平台已转移到 D&D 珠海工厂进行批量生产,最新生产数据显示,该平台的成品率为 98%,节约了 4 名操作员的劳动力成本(每年节约成本 48,000 美元)。下一步是构金属薄板壳体装配的生产机器,可以预见,实施采用这项技术的生产机器,每年可为 TE D&D 业务部门节约 52 万美元的劳动力成本。此外,这里开发的基于机器人的金属薄板壳体装配技术将显著提高 TE 在高精度水平大规模定制装配的能力,这种能力可以转而支持汽车、工业、CPD、传感器等其他业务部门的大规模定制装配自动化的发展,这肯定会在整个 TE 中产生巨大的业务影响。
致谢
开发基于机器人的金属薄板壳体装配技术是一段激动人心的旅程,开发人员非常感谢来自 TE 全球运营和 D&D 业务部门负责人的支持和赞助,特别是 Philip Gilchrist、Darel Callis、Rolando Saavedra 和 Marshall Chen 的有益建议和指导。
参考
[1] 技术参考手册 – RAPID 指令、功能和数据类型,ABB 机器人文档 M2004,rev H,RW5.15