TE 工程师讨论了与电动汽车中直流快速充电相关的车辆端热方程。
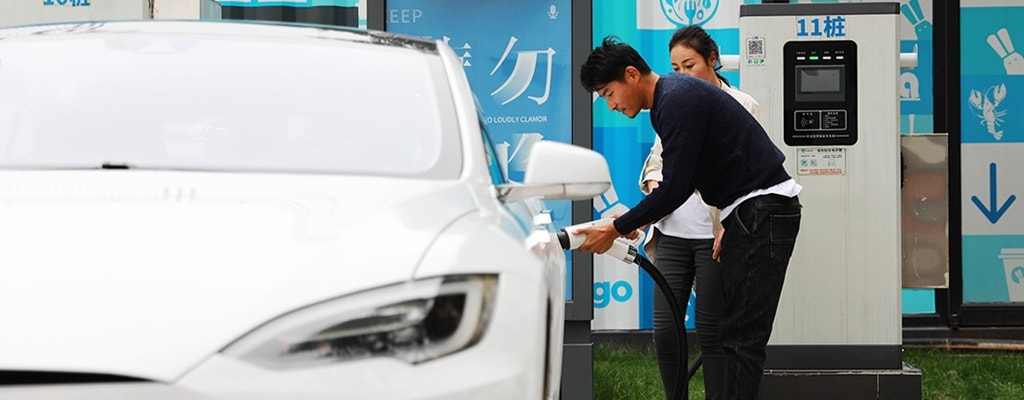
电动汽车的创新
趋势
新一代电动汽车技术
电动汽车工程师依靠互连、开关和传感器技术来推进低压数据连接网络和高压驱动系统的发展。为了实现这一目标,这些技术必须在日益集成的集中式车辆架构中并行工作。
人们常说,未来出行 - 提供更安全、更环保、更互联的交通工具,将以使用电力和数据这两类燃料的车辆为特征。然而,虽然人们对安全性、便利性和无处不在的连接的需求推动着汽车行业依赖数据的云/传感器应用不断增加,但许多消费者尽管有着环境担忧,仍不太愿意完全采用电动汽车技术。
..“在完整的电气系统中,所有连接充电点与车辆电池的导电元件……,都必须经过机械、电气以及热学设计和测量。”
驾驶员的担忧
许多潜在的电动汽车 (EV) 驾驶员主要关心的是里程和充电便利性 - 就充电时间和充电点的可用性而言。在这方面,从充电插座到电动汽车电池再到电动机的连接性和连接器元件,都对安全可靠的大功率增程快充起到了至关重要的作用,这将有助于减轻消费者的担忧。
如今,通过直流 (DC) 快速充电桩(通常在高速公路加油站可以看到)为车辆充电可能需要长达一小时的时间才能增加约 300 公里的行驶里程,具体时间取决于充电功率和电池容量。然而,行业目标是在约 10 分钟内增加 300 公里的里程,这与内燃机 (ICE) 车辆的时长或加油停留时间相当。
连接性挑战
这种大功率充电 (HPC) 在电流高达 500 安培时支持 350kW 的直流充电功率, 表示电动汽车中整个电气系统的最高负载状态。即使在硬加速的情况下,当驾驶员需要很大的功率时,也不会导致平均电流的大小相同。
由于电动汽车动力总成内所有元件(连接器、电缆)都存在固有的电阻,这种水平的持续电流会造成较高的热量损耗,当车辆不移动且没有自然对流冷却时,损耗就会进一步加剧。
因此,为了避免过载/过热,被动/主动的热量损耗或促使受控充电电流额定值降低的能力是所有导电元件设计和尺寸的关键要求。这意味着连接充电点与车辆电池的完整电气系统必须经过机械、电气以及热学设计和测量。
一个主要的挑战是,电流越高, 在相同的电压水平下,所需的电缆截面越大,传输功率就越大,且不会过热。在车辆中,这主要是重量和可用空间的问题。
例如,就成本、重量和体积来看,横截面为 50 mm2 或 95 mm2 的导线在插座和电池之间是否足够,存在相当大的差异。如果 HPC 是一个现实问题,就必须避免电缆和所有其他电气元件的尺寸过大。
迄今为止,电气元件设计并未真正反映驾驶高峰和低点之间动态变化的电流负载分布,也未反映 HPC 的要求。
现有标准基于最初用于设计继电器和(开关)保险丝的静载荷点,这些静载荷点是通过统计学方法确定的,反映它们发生的频率及其重要性这就导致采用相应的电气互连元件设计时代表静态条件的电流负载值不能反映实际情况 - 往往包含高达 20% 左右的安全裕度。
我们为混合动力及纯电动汽车提供的连接解决方案组合涵盖了整个电力动力系统系列,提供用于安全连接及保护电源所需的一整套产品,包括连接器、接头、继电器、接触器、线束和断开开关。我们在高压生成、传输和配电方面拥有数十年的技术经验,涵盖四个应用领域:高压辅助模块、高压动力系统、电池连接和充电插座。
电池连接
为了帮助让充电功率达到 350 kW 及以上的峰值负荷, 需要一种不同的方法来设计电气元件。在 TE,我们正在开发一种可以随时动态确定元件引起的温度升高和系统中热量损耗的新方法。
根据系统化和接近实际情况的热模拟技术,可以更早地检查元件设计,并预测整个整个生命周期内它在各种操作模式下的性能。这样既有利于安全地长期运行,也能在设计上改进易用性。基于模型的热模拟技术为未来的负载型态提供了可验证的基础,这有助于证明高压/高电流路径上所有互连元件的安全性、可靠性和耐用性。
如同内燃机 (ICE) 被视为传统机动车辆的心脏,电池也被视为电动汽车的心脏,在这一领域出现了许多相同的设计难题。
电池电动汽车 (BEV) 的动力系统需要更多的电力。这就对物理层中汽车板网的集成提出了挑战,有时各项要求之间会互相矛盾。
新一代的电动汽车动力系统连接设计将引入充电插座、高压连接器、继电器和接触器以及用于电动汽车电池管理系统的微型低压连接器。
了解与汽车典型信道建立高速连接的选项,同时将环境影响考虑在内,通过实际案例了解使用模拟工具分析信道的紧迫性。
在所有车辆操作模式下,电力必须安全地进出电池。 因此,主电池连接以及某些情况下的电池模块连接,必须能够在大功率充电周期内传输高达 600 安培的电流数分钟,在硬加速期间传输更高的峰值水平。
电池模块连接还构成电池保护(过热关闭)、电池管理(电荷态,例如充电状态 (SoC))和电池平衡(不同 SoC 级别的电池之间的充电电压均衡)的物理层。为了确保这些操作,每个单独的电池模块都必须具有防故障电气连接。
这需要高度集成的接触系统不仅能够在车辆的整个使用寿命(例如 300,000 公里/10 年)中支持全部功能,而且还必须足够坚固,能够防止振动和温度应力对触点的机械和电气性能产生不利影响。此外,触点还必须完全接触安全,以消除潜在的高压和高功率危险,并确保制造商和服务人员的安全。
例如,TE BCON+ 模块连接器系统的主要设计目标是处理 400 安培(短时峰值高达 1,200 安培)的恒定电流以及高达 1,000 V 的电压,并在 -40 °C 至 +80 °C 的典型电池环境温度下可靠运行。主要挑战是最大限度地降低每个接触点的接触电阻,确保尽可能减少功率损耗和热应力,并通过符合全球 OEM 规格的高抗振性电阻在整个使用寿命中保持可靠。
电池管理
电池管理系统是电子系统 管理电池组的充电和内部电池的放电。它通过监测电池模块的温度和电压信号以及电池组级别的电流信号,并将它们传输到平衡或控制电池模块环境的元件,防止电池在安全限值之外运行。
电池管理系统对电池的最佳性能和安全性至关重要,这意味着它必须以极高的精确度和可靠性运行,且必须具有高度坚固的结构。但是,它也必须紧凑轻巧,在整体的电池组几何结构中融合尽可能小的体积。
连接也是电池管理的关键推动因素。它需要将信号传输到电池管理控制器 (BMC),在那里处理这些信号并将其发送到电池管理控制器 (CMC),从而平衡电池并控制电流(例如在充电期间)。
BMS 电子器件需要高度紧凑且灵活的连接器系统。鉴于电池与电池控制器的比率因电池设计要求(如容量和车辆能量需求)而异,连接器系统必须能够灵活适应连接器结构的多种排列。连接器还应能够灵活支持不同类型的电缆,包括 FFC/FPC(扁平柔性/印刷电缆),这些电缆可以布置在紧凑复杂的电池几何形状周围。
此外,连接器系统在引脚之间需要一个安全的“漏电”和间隙距离,确保不会因灰尘污染或电弧导致短路而发生故障风险。由于电池模块是作为密封元件提供的,因此制造商必须确保所有内部连接器都符合汽车级坚固性和可靠性的严格要求。
特色电源和数据解决方案
理解新一代出行连接解决方案。 由电缆和连接器组成的物理电源和数据网络层将发挥重要作用,它们将成为消费者希望拥有、驾驶或乘坐的新一代互连车辆的支柱,这些车辆更安全,也更环保。
这意味着低压数据连接网络和高压 (HV) 驱动系统必须在日益集成的集中式(“智能”)架构中并行、高度可靠且安全地工作。
互连、开关和传感器技术将成为实现这一目标的关键创新因素。凭借在这些领域广泛领先的产品组合和专业知识,我们可以与汽车技术公司携手打造新一代出行连接解决方案。
作者
- Qiong Sun,全球汽车混合动力与电动汽车解决方案副总裁
- Uwe Hauck,汽车混合动力与电动汽车解决方案产品管理总监
- Luis Puras Trueba,汽车混合动力与电动汽车解决方案产品管理高级经理
- Chris Yeadon,汽车混合动力与电动汽车解决方案产品市场高级经理