过程内微米级精确度厚度检测平台
摘要
厚度是关键的制造参数,直接影响基板的性能。由于缺乏过程内检测方法,目前的离线检测方法需要进行破坏性检测,而且每次产品转换成本约为数百美元。我们开创了一个厚度检测平台,可执行过程内、达微米级精确度、非接触式的动态检测。
问题陈述
基板是一种重要的产品,是许多芯片产品的基本元件之一。基板产品由三层组成。两个金属层和一个正温度系数 (PTC) 层被层压在一起。图 1 显示了基板制造过程的示意图。厚度是基板质量最重要的参数,直接影响到性能。如果最终产品的厚度不达规,我们没有返工机会,必须放弃所有产品。
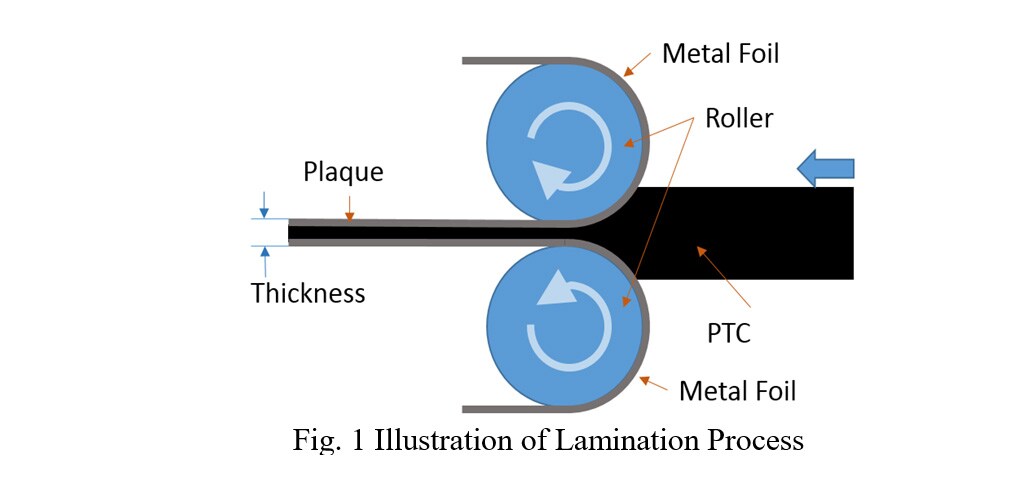
在实际生产中,操作员需要调整两个滚子之间的距离,以控制厚度。问题往往出现在转换过程中。在整个产品系列中,存在 9 种不同厚度的部件的编号。通常情况下,厚度会频繁发生变化,每天转换两次。
转换的成本非常高。由于没有在线厚度检测设备,当前转换基于离线检测。操作员需要首先生产一些样品,停止机器,切下样品进行离线破坏性检测。操作员将重复这个过程,直到得到满意的结果。这是手动微米级调整,难度很高且耗时。
要开发一个在线基板厚度检测系统,应考虑解决三个难题:
1) 微米级精确度
2) 动态检测
3) 非接触式检测
我们开创了一个厚度检测平台,可执行过程内、达微米级精确度、非接触式的动态检测。我们使用激光技术来执行非接触式检测。为了达到精确度要求,我们进行了一次 DoE,以了解动态检测的关键影响因素是什么,以及如何实现动态检测的精确度要求。平台通过了 GR&R 认证。
方法和结果
平台概述
图 4 显示了大致的平台构成:紫色部分表示基板。两个激光传感器,一个向上,一个向下,安装在一个 C 形传感器安装框架中,它们配合运行以执行厚度检测。由伺服电机驱动的两个轴来回移动 C 形框架。 轴安装在大理石框架上,以提高稳定性。大理石通常用作高精度测量系统(例如协调测量机)底座。 大理石框架下面是电气控制柜。
开始进行生产后,基板连续向 X 方向经过检测站,向上的激光传感器和向下的激光传感器沿 Y 方向移动,形成一个锯齿形的检测轨迹,如图 4 下方所示。
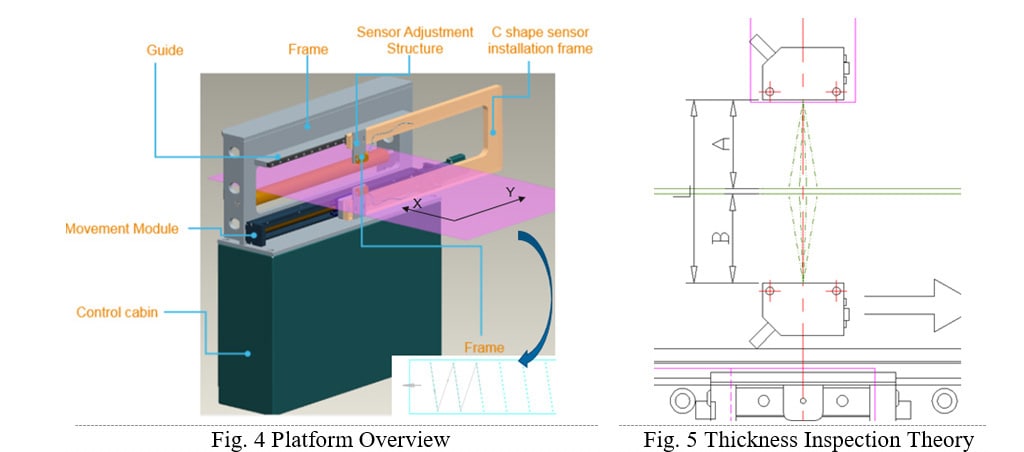
基于两个传感器的厚度检测理论如图 5 所示。两个激光传感器用于检测传感器与物体之间的距离。L 为两个传感器之间的距离,A 是由向上的激光传感器测量的距离,B 是由向下的激光传感器测量的距离,基板的厚度为
厚度 = L-A-B (1)
基于机器人的 DoE 平台
为了在实际生产中应用方程 (1),我们需要确保在检测过程中检测环境完全满足方程 (1) 的条件。然而,实际制造环境中存在着各种噪声资源,包括激光传感器的误差、基板振动、基板旋转、传感器运动和产品运动,因此很难直接应用方程 (1)。
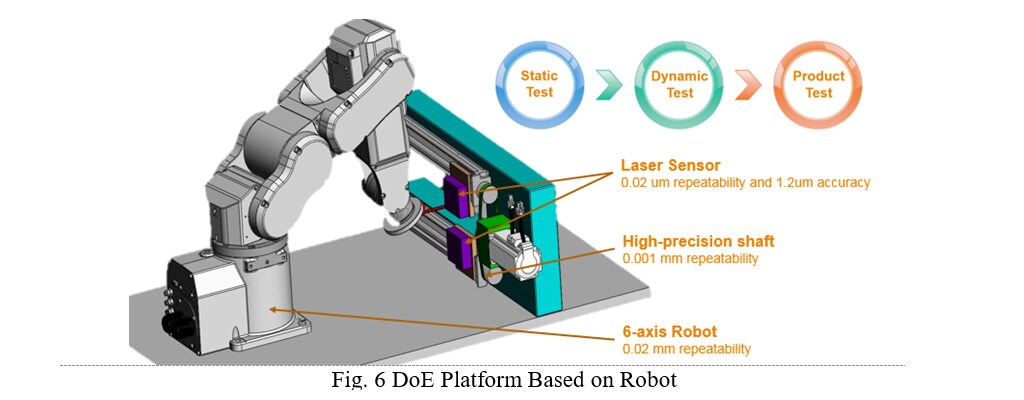
我们建立了一个 DoE 平台,用于分析每个影响因素的影响。DoE 平台基于一个 6 轴机器人,重复性为 0.02 mm。操纵装置末端的夹子可以操纵基板样品,模拟振动、旋转、垂直运动和水平运动。除机器人外,高精度激光传感器作为一种关键设备,具有 0.02 微米的重复性和 1.2 微米的精确度。水平移动传感器的轴具有 0.001 mm 的重复性。系统的固有精确度足以满足要求。但是,外部环境可能会降低固有精确度,因此该 DoE 的目的是找到减少影响和恢复固有精确度的方法。
我们进行了三种实验:
- 静态测试:产品和传感器都是静态的,以测试系统的重复性和精确度。这是系统的固有精确度
- 动态测试:测试产品旋转、振动、产品水平运动和产品垂直运动的影响,并找出各因素与精确度之间的关系
- 真实产品测试:真实产品 GR&R 认证
讨论及要点
本文介绍了有关一个过程内微米级精度检测平台的创新,内容包括平台概述,非接触式激光技术,动态检测校准算法,软件和 GR&R 认证。我们详细阐述了如何在 DoE 实验和科学分析的基础上提高系统精确度。
该平台的优势包括过程内、微米级精确度、动态和非接触式的特点。检测平台直接集成到制造生产线中,并向操作员显示实时检测数据。该系统的检测精确度达到微米级,通过了 GR&R 认证。动态检测可用于各种各样的产品。我们以激光技术为基础,实现了非接触式检测。
该平台有望在将来用于需要厚度检测的其他类型的产品,同时,该平台可以进行改进,以覆盖更快的生产线和更广泛的产品。
过程内微米级精确度厚度检测平台
摘要
厚度是关键的制造参数,直接影响基板的性能。由于缺乏过程内检测方法,目前的离线检测方法需要进行破坏性检测,而且每次产品转换成本约为数百美元。我们开创了一个厚度检测平台,可执行过程内、达微米级精确度、非接触式的动态检测。
问题陈述
基板是一种重要的产品,是许多芯片产品的基本元件之一。基板产品由三层组成。两个金属层和一个正温度系数 (PTC) 层被层压在一起。图 1 显示了基板制造过程的示意图。厚度是基板质量最重要的参数,直接影响到性能。如果最终产品的厚度不达规,我们没有返工机会,必须放弃所有产品。
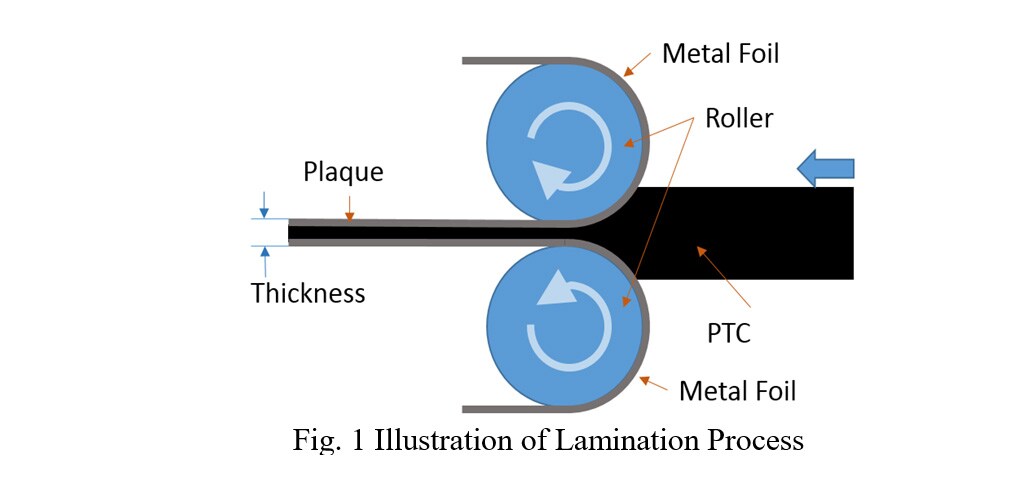
在实际生产中,操作员需要调整两个滚子之间的距离,以控制厚度。问题往往出现在转换过程中。在整个产品系列中,存在 9 种不同厚度的部件的编号。通常情况下,厚度会频繁发生变化,每天转换两次。
转换的成本非常高。由于没有在线厚度检测设备,当前转换基于离线检测。操作员需要首先生产一些样品,停止机器,切下样品进行离线破坏性检测。操作员将重复这个过程,直到得到满意的结果。这是手动微米级调整,难度很高且耗时。
要开发一个在线基板厚度检测系统,应考虑解决三个难题:
1) 微米级精确度
2) 动态检测
3) 非接触式检测
我们开创了一个厚度检测平台,可执行过程内、达微米级精确度、非接触式的动态检测。我们使用激光技术来执行非接触式检测。为了达到精确度要求,我们进行了一次 DoE,以了解动态检测的关键影响因素是什么,以及如何实现动态检测的精确度要求。平台通过了 GR&R 认证。
方法和结果
平台概述
图 4 显示了大致的平台构成:紫色部分表示基板。两个激光传感器,一个向上,一个向下,安装在一个 C 形传感器安装框架中,它们配合运行以执行厚度检测。由伺服电机驱动的两个轴来回移动 C 形框架。 轴安装在大理石框架上,以提高稳定性。大理石通常用作高精度测量系统(例如协调测量机)底座。 大理石框架下面是电气控制柜。
开始进行生产后,基板连续向 X 方向经过检测站,向上的激光传感器和向下的激光传感器沿 Y 方向移动,形成一个锯齿形的检测轨迹,如图 4 下方所示。
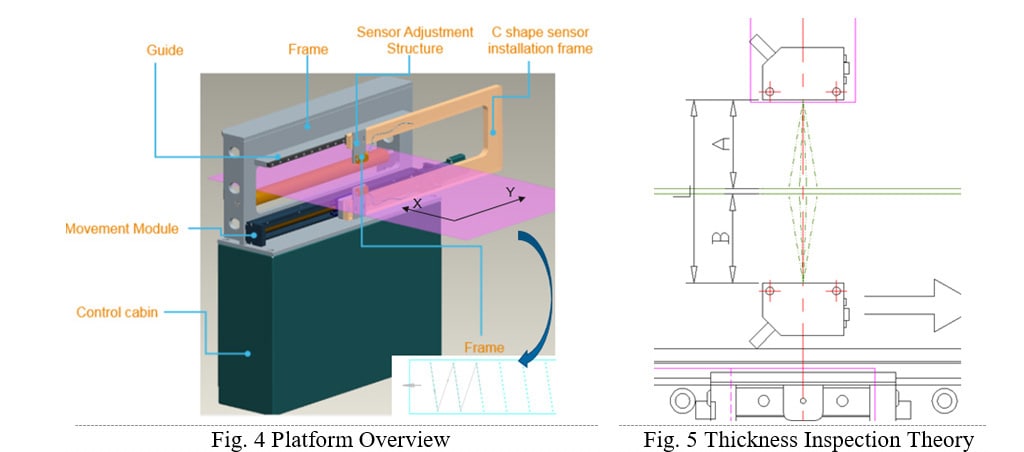
基于两个传感器的厚度检测理论如图 5 所示。两个激光传感器用于检测传感器与物体之间的距离。L 为两个传感器之间的距离,A 是由向上的激光传感器测量的距离,B 是由向下的激光传感器测量的距离,基板的厚度为
厚度 = L-A-B (1)
基于机器人的 DoE 平台
为了在实际生产中应用方程 (1),我们需要确保在检测过程中检测环境完全满足方程 (1) 的条件。然而,实际制造环境中存在着各种噪声资源,包括激光传感器的误差、基板振动、基板旋转、传感器运动和产品运动,因此很难直接应用方程 (1)。
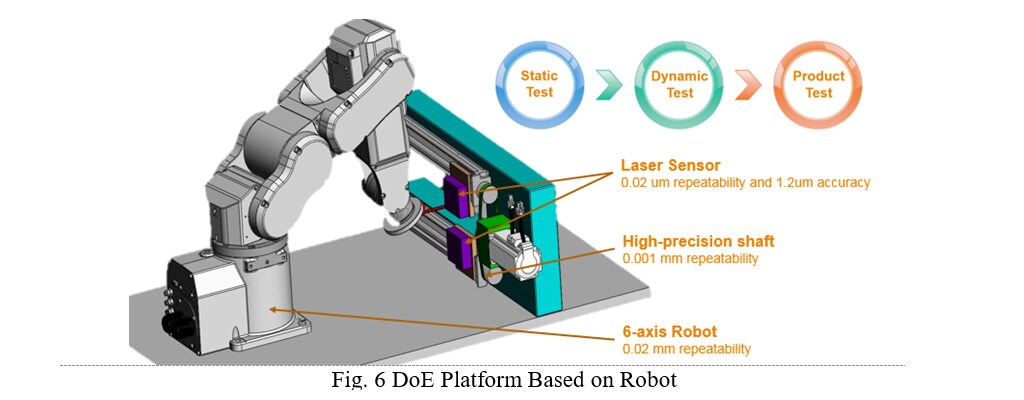
我们建立了一个 DoE 平台,用于分析每个影响因素的影响。DoE 平台基于一个 6 轴机器人,重复性为 0.02 mm。操纵装置末端的夹子可以操纵基板样品,模拟振动、旋转、垂直运动和水平运动。除机器人外,高精度激光传感器作为一种关键设备,具有 0.02 微米的重复性和 1.2 微米的精确度。水平移动传感器的轴具有 0.001 mm 的重复性。系统的固有精确度足以满足要求。但是,外部环境可能会降低固有精确度,因此该 DoE 的目的是找到减少影响和恢复固有精确度的方法。
我们进行了三种实验:
- 静态测试:产品和传感器都是静态的,以测试系统的重复性和精确度。这是系统的固有精确度
- 动态测试:测试产品旋转、振动、产品水平运动和产品垂直运动的影响,并找出各因素与精确度之间的关系
- 真实产品测试:真实产品 GR&R 认证
讨论及要点
本文介绍了有关一个过程内微米级精度检测平台的创新,内容包括平台概述,非接触式激光技术,动态检测校准算法,软件和 GR&R 认证。我们详细阐述了如何在 DoE 实验和科学分析的基础上提高系统精确度。
该平台的优势包括过程内、微米级精确度、动态和非接触式的特点。检测平台直接集成到制造生产线中,并向操作员显示实时检测数据。该系统的检测精确度达到微米级,通过了 GR&R 认证。动态检测可用于各种各样的产品。我们以激光技术为基础,实现了非接触式检测。
该平台有望在将来用于需要厚度检测的其他类型的产品,同时,该平台可以进行改进,以覆盖更快的生产线和更广泛的产品。